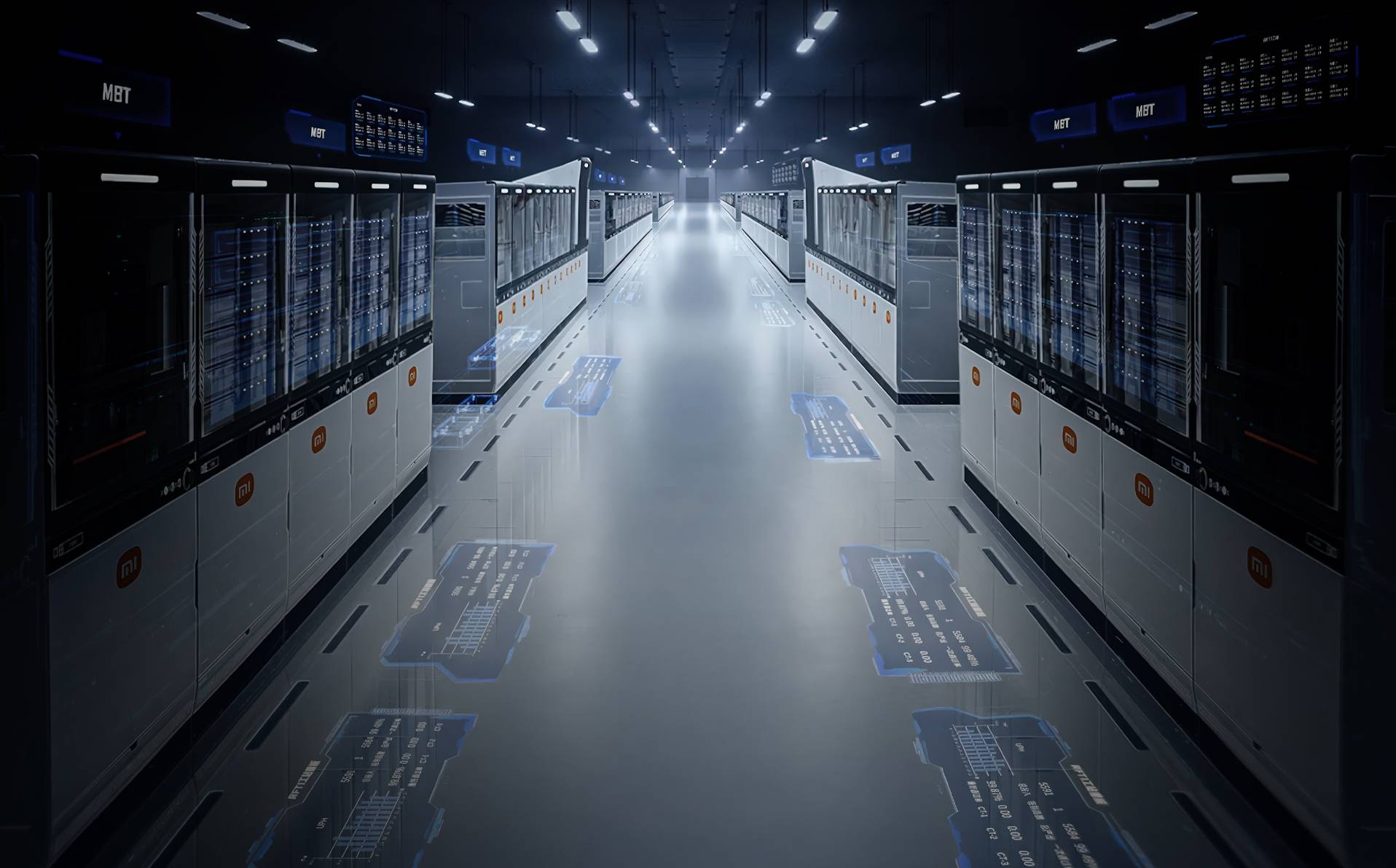
À l’intérieur de la première dark factory
Un smartphone toutes les 3 secondes, sans aucune intervention humaine ! À Changping, en Chine, une usine de 80 000 m2 entièrement automatisée vient d’être inaugurée. Au point qu’il n’y a même plus besoin d’allumer la lumière…
De longs couloirs, des machines, des machines et encore des machines qui travaillent non-stop, 24 heures sur 24, 7 jours sur 7, dans le noir, avec juste des LED qui clignotent un peu partout. Pas un humain dans les parages. Bienvenue à l’intérieur de l’usine la plus récente de Xiaomi, le deuxième plus gros constructeur de smartphones dans le monde derrière Samsung.
Autant le dire tout de suite, aucun journaliste d’Epsiloon n’a pu entrer dans ces lieux – Xiaomi n’a d’ailleurs même pas souhaité répondre à nos questions. Mais en juillet dernier, blouse blanche et casquette stérile sur la tête, Lei Jun, le PDG de l’entreprise, a proposé en deux courtes vidéos une rapide visite de cet endroit monumental de 80 000 m2. “Ici, 100 % des process clés seront désormais automatisés”, “10 millions de téléphones portables y seront fabriqués chaque année sur 11 lignes de production”. Le dirigeant reconnaît qu’il reste une salle de contrôle avec quelques personnes pour reprendre la main, au cas où, mais il l’assure : ses robots-machines sont capables de résoudre des problèmes, d’optimiser des commandes, voire d’évoluer par eux-mêmes.
C’est Star Wars
Changping est l’exemple le plus spectaculaire d’un nouveau genre d’usine, la “dark factory”, une “usine sombre” où la fabrication est automatisée de bout en bout de manière évolutive – et où il n’y a plus besoin d’allumer la lumière puisque seules des machines y travaillent. L’étape ultime de l’automatisation ? L’écrivain Philip K. Dick avait décrit en 1955 dans une nouvelle, Autofab, un monde avec des usines autonomes. Mais c’était de la SF…
C’est une étape symbolique, le passage du monde des automates au monde de l’IA
Xavier Comtesse, chercheur suisse en informatique
Au milieu du XVIIIe siècle, la fameuse machine à vapeur de la première révolution industrielle avait automatisé la puissance de travail ; en 1913, la chaîne de montage des usines Ford avait automatisé le déplacement des pièces vers les ouvriers ; en 1961, le bras articulé d’Unimate, le premier robot industriel de General Motors, avait automatisé la manipulation des pièces. Mais les humains sont toujours restés autour des chaînes de montage. “L’étape que l’on vit actuellement avec l’arrivée des dark factories est très symbolique : elle montre le passage d’un monde déterministe, avec des automates, à un monde de plus en plus probabiliste, avec l’IA”, pose Xavier Comtesse, chercheur suisse en informatique, à la tête d’un think tank consacré à ce sujet.
Réduction de coûts
“Je ne suis pas surpris par cette annonce de Xiaomi, confie de son côté Zhiguo Zeng, un chercheur chinois qui travaille à l’école CentraleSupélec sur l’automatisation et la résilience des lignes de production. En Chine, beaucoup d’entreprises sont en train d’implémenter des dark factories, comme Midea, Chery, Foxconn… Toutes ces équipes font ça dans une optique de réduction de coûts, puisque cela implique moins de salariés.”
C’est Fanuc, une entreprise japonaise spécialisée dans la fabrication de robots, qui a testé la première le concept, dès les années 1990 : une ligne d’usinage de pièces pour robots de 200 m de long sur 100 m de large. “Quand on entre dans ce bâtiment, cela fait un drôle d’effet, c’est Star Wars, avec des rampes de mini-lumières partout, c’est assez impressionnant. Et pourtant, ce n’est pas du cinéma, décrit Nicolas Couche, qui travaille pour une branche de Fanuc en France. Aujourd’hui, cela a été optimisé et copié dans d’autres usines d’usinage de notre entreprise, les pièces entrent d’un côté et sortent finies de l’autre. On arrive à cumuler dans nos bâtiments 900 heures de production sans intervention humaine.”
Repousser les limites
Peu d’entreprises dans le monde sont pour l’instant allées aussi loin. Et Xiaomi est la première à se lancer avec une telle envergure. “Les pionniers de ce concept sont ceux qui repoussent les limites de l’automatisation, de l’intelligence artificielle et de la robotique, comme Fanuc, Tesla, Rethink Robotics ou Amazon, liste Philip Gisi, ingénieur américain, spécialiste des process industriels. Nous sommes clairement dans une période de transition. Nous avons désormais les moyens techniques de réaliser ces usines, mais il y a encore de nombreux obstacles.”
Pour l’instant, une dark factory est efficace quand tout va bien
Zhiguo Zeng, chercheur à l’école CentraleSupélec
Car malgré les annonces de Xiaomi sur sa capacité à faire face à des pannes ou à des changements en cours de production de manière autonome, malgré les progrès de l’IA, de la modélisation et de la puissance de calcul, sortir totalement l’humain de l’équation de la production industrielle reste un défi. “Pour l’instant, une dark factory est efficace quand tout va bien et que tout est conforme au plan de départ, mais quand il y a le moindre obstacle ou imprévu, et qu’il faut changer un plan de production, on se rend compte que le système n’est finalement pas si flexible ni si adaptable que cela. Et que les humains restent plus agiles que les machines”, prévient Zhiguo Zeng.
Un mea culpa
C’est ce qu’a constaté aussi Xavier Comtesse, en avril dernier, lorsqu’il s’est rendu au Japon avec un groupe d’experts pour visiter plusieurs sites très automatisés, dont celui de Fanuc : tout ne fonctionnait pas si bien. “Pendant notre passage, des lampes rouges se sont allumées plusieurs fois et on a vu des techniciens qui ont dû intervenir pour réparer !”, témoigne-t-il.
Le cas d’école est l’usine de Tesla, à Fremont, aux États-Unis, inaugurée en 2018. Son célèbre patron, Elon Musk, décide de construire un site parmi les plus robotisés du monde pour fabriquer sa Model 3. Après plusieurs mois de test, il se rend compte que des problèmes techniques se multiplient sans que l’on puisse y faire face, que la productivité n’est pas à la hauteur et que les coûts de production augmentent. Il fait marche arrière et revient à une fabrication en partie manuelle, déclarant : “L’automatisation excessive chez Tesla a été une erreur. Pour être précis, mon erreur. Les humains ont été sous-estimés.”
La clé des jumeaux numériques
“À part quelques exemples très avancés, on est dans une époque intermédiaire que l’on pourrait qualifier de ‘grey factory’”, estime Yohann Mesmin, directeur de la transformation digitale chez Siemens. Mais il en est convaincu : “La clé qui va permettre d’aller plus loin en matière d’autonomie tient à l’utilisation de plus en plus maîtrisée des jumeaux numériques.” L’idée : avoir des représentations virtuelles en 3D des machines, des lignes de production, voire de l’usine tout entière, enrichies d’un maximum d’éléments, afin de programmer la chaîne, de l’optimiser et d’anticiper les pannes, les imprévus…
Guillaume Vendroux, directeur de Delmia, chez Dassault Systèmes, explique : “Il faut réussir à stresser virtuellement une ligne de toutes les façons possibles pour anticiper ce qui pourrait se passer et renforcer la robustesse du système. On crée par exemple des défauts que l’IA va apprendre à gérer et à partir desquels elle pourra faire des corrélations de situations. Grâce à quoi, par exemple, des constructeurs automobiles comme Honda n’ont plus besoin de prototype physique.”
“On essaie maintenant de faire évoluer nos jumeaux en récupérant des données du terrain pour converger vers un métavers industriel”, complète Yohann Mesmin. Qui ajoute que Siemens travaille pour rendre ses sites industriels (plus de 120) de plus en plus autonomes. Beaucoup de nouvelles dark factories en perspective…
La place de l’humain
Mais avec quels résultats à la clé ? En termes de coûts ? De productivité ? D’organisation du travail ? De perte d’emplois ? De bilan énergétique ? De bilan carbone ? Vu le faible nombre de dark factories en activité, peu de chiffres sont disponibles pour le moment. Selon l’expert de Siemens, “les premières estimations de retour sur investissement pourraient se situer entre 15 et 20 % par an, lié à une réduction de la main-d’œuvre et à l’optimisation énergétique. Des usines automatisées ont démontré une baisse de 30 à 40 % des coûts de production, avec des gains de productivité allant jusqu’à 50 %”. Avec l’annonce du remplacement de certains métiers par d’autres : moins de manutention et plus de data scientists.
Question d’adaptabilité
Tout le monde s’accorde cependant à dire que l’ultra-automatisation n’est et ne sera pas valable ni intéressante pour toutes les activités industrielles – toutes les usines n’ont pas vocation à éteindre la lumière. Par exemple, plus on automatise un site, plus la production est rigide. “Si on veut aller petit à petit vers ce qu’on appelle la personnalisation de masse, c’est-à-dire la fabrication d’objets sur mesure, on voit bien que la dark factory ne conviendra pas”, souligne Guillaume Vendroux.
Le niveau de confiance que l’on va mettre en place derrière la machine est un des gros enjeux aujourd’hui
Guillaume Vendroux, directeur de Delmia, chez Dassault Systèmes
Zhiguo Zeng s’est penché de son côté sur l’automatisation d’une entreprise qui travaille autour de la taille de pierres d’ornement, et qui a cumulé des machines provenant de différents fabricants. Il s’est rendu compte que l’activité avec moins d’humains devenait moins rentable. Une manière de rappeler que les machines et l’IA ne peuvent pas encore rivaliser avec la capacité d’adaptation humaine.
Nouveau point de départ
En fait, les dark factories semblent utiles pour produire des objets qui ne sont pas trop sensibles d’un point de vue de la sécurité, dans des volumes élevés et avec une forte rentabilité. Autrement dit, des smartphones plutôt que des portes d’avion. “Le niveau de confiance que l’on va mettre en place derrière la machine est un des gros enjeux aujourd’hui”, reconnaît Yohann Mesmin. Guillaume Vendroux renchérit : “Toutes les activités de contrôle qualité restent compliquées pour une dark factory, car une IA n’est pas infaillible. Sans oublier la question de la cybersécurité : dans une usine qui fabrique des objets sensibles, on ne pourra pas se permettre de se faire hacker.”
“Cette automatisation à 100 % pose clairement la question de la criticité, c’est-à-dire de l’importance et de la disponibilité d’un système, témoigne Anne Barros, chercheuse en génie industriel qui travaille sur l’usine du futur à CentraleSupélec. La résilience en cas de panne est potentiellement problématique. Les industriels reviennent vers nous et nous le disent déjà.”
“Finalement, on aurait pu penser que la dark factory allait être le point ultime, le point final de l’usine. Ce n’est pas le cas. Il semblerait plutôt que ce soit un nouveau point de départ où humains et machines vont se repartager les activités, en fonction des objectifs recherchés”, analyse Maria Sokhn, informaticienne et professeure à la Haute École spécialisée de Suisse occidentale, qui a visité elle aussi des installations de Fanuc. En attendant, l’usine de Changping tourne. Le temps de lire cet article, elle devrait avoir produit 200 smartphones, lumière éteinte – ou presque.